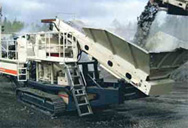
Efficiency of grinding stabilizers in cement clinker processing
2013.4.1 Clinker grinding represents the most energetically demanding part of the production process and grinding stabilizers (very often known as “grinding activators”,
More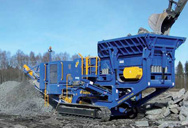
Effect of clinker grinding aids on flow of cement-based
2014.9.1 Abstract. Grinding aids (GAs) are increasingly used during cement production to reduce energy consumption and/or optimize clinker factor. This paper
More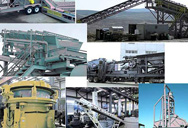
Modernizing cement manufacturing in China leads to
2022.11.17 The cement manufacturing process mainly includes four steps: resource extraction, raw material preparation, clinker calcination, cement grinding 17, 18, and
More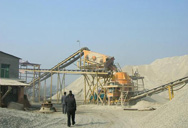
Influence of Clinker Microstructure on Grinding Efficiency in
2020.7.31 Grinding processes in cement production technology are quite energy-intensive. The mechanism of action of surfactants on the course of the clinker grinding
More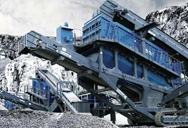
Resistance to Grinding and Cement Paste Performance of
2021.4.19 Herein, we evaluate experimentally the interactions among clinker, limestone and gypsum during the final grinding stage in Portland cement production. We
More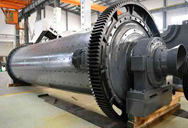
Overview of cement clinker grinding - ResearchGate
2023.1.1 Download Citation On Jan 1, 2023, Vipin Kant Singh published Overview of cement clinker grinding Find, read and cite all the research you need on ResearchGate.
More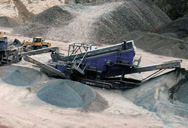
Use of cement grinding aids to optimise clinker factor
2010.1.1 A comprehensive research project was undertaken to evaluate the effect of grinding aids (GAs) on the percentage of clinker decrease and reduction of energy
More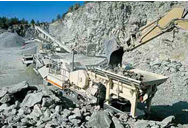
Understanding the Role of Clinker Grinding in Cement
2023.10.19 Clinker grinding is a vital and integral process in cement production, playing a crucial role in transforming clinker into the final cement product. Here’s an
More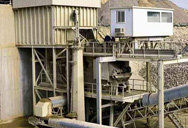
(PDF) Clinker grinding process and cement
2015.9.16 Clinker grinding process and cement properties improvements by additives. Conference: 19th International Baustofftagung. Authors: Marco Goisis. ITALCEMENTI. Claudia
More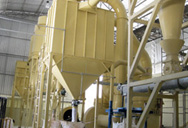
What is Cement Clinker? Composition, Types Uses
6 天之前 Clinker is a nodular material produced in the kilning stage during the production of cement and is used as the binder in many cement products. The lumps or nodules of clinker are usually of diameter 3-25 mm and dark grey in color. It is produced by heating limestone and clay to the point of liquefaction at about 1400°C-1500°C in the rotary ...
More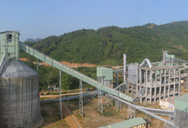
Cement Clinker Grinding Aids - 911 Metallurgist
2016.7.12 Effect of Grinding Aids on Wet Grinding. A variety of additives have been shown to have grinding aid characteristics for grinding cement clinker. Typical among these are amines, organosilicones, glycols, resins, cod oil, kojic acid, carbon blacks, wool grease, calcium sulfate, urea, asphaltenes, etc. Figure 4-26 shows a typical comparison ...
More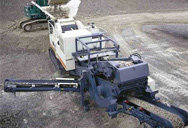
Understanding the Role of Clinker Grinding in Cement
2023.10.19 Clinker grinding in cement manufacturing is a critical process, but it comes with its fair share of challenges. This section explores the common challenges faced in clinker grinding and presents potential solutions and best practices to address them. Energy Consumption: ...
More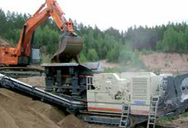
(PDF) Clinker grinding process and cement properties
2015.9.16 Abstract. Sustainability of cement products is increased by reducing grinding energy and limiting CO2 emissions. Cement additives permit to reach bothe the targets. Grinding Aids reduce particle ...
More
Clinker Grinding Unit Station Plant vs. Cement production
2023.10.8 A clinker grinding plant is a facility where the essential raw material for cement production, known as clinker, is ground into a fine powder. Clinker grinding plants offer a streamlined ...
More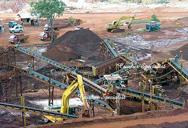
Efficiency of grinding stabilizers in cement clinker processing
2013.4.1 The diameter of the grinding chamber D = 200 mm was the same as its length L. The mill chamber was constructed of porcelain and the grinding body stock consisted of 133 corundum balls of 25.1 mm diameter and 11,500 steel beads of 4.9 mm diameter.The grinding stock formulation arose as a result of many years development of
More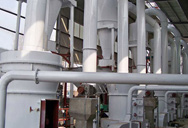
Cement Grinding Unit - Clinker Grinder AGICO Cement
The cement grinding unit manufactured by our company merges drying, grinding, powder classifying, dust collecting and cement packing into a single. It can not only grind cement clinker but also process cement admixture, such as gypsum, fly ash, furnace slag, coal gangue, etc., realizing a stable, high-quality and automated cement production.
More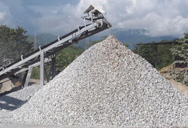
Overview of cement clinker grinding - ResearchGate
2023.1.1 This paper presents a study on the production of high-volume fly ash (HVFA) blended cements incorporating an ASTM Type III cement clinker, three ASTM Class F fly ashes and a superplasticiser. The ...
More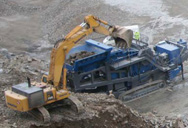
Cement Clinker Grinding Plant - ball mills supplier
The cement grinding station does not produce clinker and processes cement through purchased clinker. Unlike cement clinker production lines that rely on raw materials in mining areas, independent production clinker grinding units are mainly located around major cement sales markets, that is, near large and medium-sized cities.
More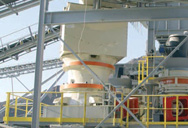
Effect of Grinding Aids in Cement Grinding - IOPscience
2018.8.1 Grinding aid or grinding additives refer to substances which when mixed into the mill contents cause an increase in rate of size reduction and flowability. Grinding process of clinker was carried on with a laboratory scale ball mill by varying different type of grinding additives and dosage while the operating conditions of the mill was kept ...
More
Laxmi Engineers - Cement Clinker Grinding Plant
Welcome to our Website. Laxmi Engineers, a reputable manufacturer and supplier of a wide range of cement plants, packing machines, industrial crushers, feeder machines, and other items, was established in 1991. These machines were made by our trained professionals using top-notch raw materials and cutting-edge technology in Jodhpur, Rajasthan.
More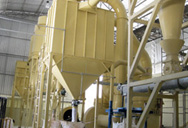
Portland cement clinker - Understanding Cement
Portland cement clinker - overview. Portland cement clinker is a dark grey nodular material made by heating ground limestone and clay at a temperature of about 1400 °C - 1500 °C. The nodules are ground up to
More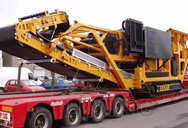
Influence of the clinker SO3 on the cement characteristics
2011.8.1 The hardness of the clinker samples correlated with the clinker SO 3.This related to the influence of SO 3 on the ratio of C 3 S/C 2 S in the clinker (Fig. 1) and on alite crystal size (Table 4).In order to obtain a similar fineness (Blaine 3600 ± 50 cm 2 /g), the time, for grinding the clinker with relatively high SO 3, was extended.The residue of the
More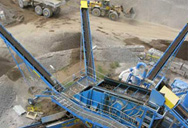
Cement - Extraction, Processing, Manufacturing Britannica
There are four stages in the manufacture of portland cement: (1) crushing and grinding the raw materials, (2) blending the materials in the correct proportions, (3) burning the prepared mix in a kiln, and (4) grinding the burned product, known as “ clinker,” together with some 5 percent of gypsum (to control the time of set of the cement). The three processes of
More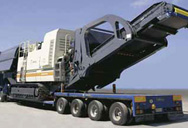
CLINKER GRINDING IN CEMENT PRODUCTION
2019.2.21 Earlier we considered a mixture of which materials is used in cement production. The base of this mixture is a clinker. In this article, we will consider the composition of clinker and its impact on grinding balls deterioration in milling process. Clinker (in cement industry) is transitional product in cement production. Upon heating
More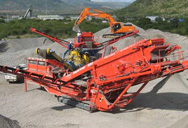
Clinker size and cement grinding GCP Applied Technologies
2021.2.11 As a general rule, there should be less than 25% of clinker that is below 1mm in size. Coarse clinker is more of an issue for ball mills. Some cement groups use a formula, such as Bond’s, to calculate the maximum ball size required in a ball mill, based on the average size of the clinker feed. However, one drawback with this approach is that ...
More
HeidelbergCement raises clinker, grinding capacity - Indian Cement
October 14, 2021. By. admin. To raise its all-India production capacity to about 6 million tonne per annum (mtpa) from 3.1 mtpa Heidelberg Cement India has completed investments of Rs 1,500 crore. On the company announced that it has enhanced clinker capacity to 3.1 mtpa from 1.2 mtpa and cement grinding capacity to two mtpa (one mtpa) at Imlai ...
More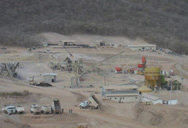
Cement Clinker: Production, Composition, Types, and Impact
2023.6.6 Production Process of Clinker. Cement manufacturers create clinkers through a multi-step process that includes ingredient selection, heating, and grinding. Raw Mineral Preparation – The main ingredients in clinker production are limestone and clay. Producers quarry these ingredients, transport them to the production facility, and then
More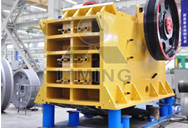
Use of cement grinding aids to optimise clinker factor
2010.1.1 A comprehensive research project was undertaken to evaluate the effect of grinding aids (GAs) on the percentage of clinker decrease and reduction of energy needed during the grinding process. Three GAs, based on amines, glycols and acids, were tested at various concentrations. The tested cement properties include water demand, Blaine
More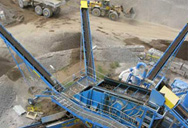
Know All About Cement Manufacturing Process in India mycem cement
1 天前 Clinker grinding along with gypsum – Cement. Grinding. Storing. Packing. Process Description . Mining and Raw Material Preparation . The prime raw material limestone after blasting in mines is broken into big boulders. Then it is transported by dumpers, tipplers to limestone crusher where it is crushed to 15 to 20mm size.
More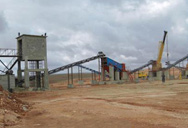
Plants JK Cement
JK Cement Works, Panna. JK Cement Works, Panna - Wholly owned subsidiary of JK Cement Ltd. is situated in the Central region of India in Panna District, Madhya Pradesh. The plant was commissioned and
More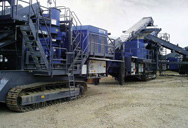
What is Clinker? (Meaning, History,
Ordinary Portland Cement Clinker is the essential component in producing cement which is made by sintering limestone.In the manufacture of Cement, clinker formed by sintering or fusing without melting to the
More
Resistance to Grinding and Cement Paste Performance of
2021.4.19 Grinding of finished cement is performed in a single stage, intergrinding materials with very different grindabilities. This intergrinding process has many different interactions among the different components of the finished cement. In a context of developing more sustainable and less energy intensive processes, it is important to
More
The occurrence of MgO and its influence on properties of clinker
2021.7.26 The structure of periclase crystals is the most important factor affecting delayed expansion [16].Reducing the size of periclase particles [17], [18] as well as the largest–to–smallest diameter ratio [18], finely grinding raw meal and cement [19], and uniformly distributing periclase crystals [19] are important methods of curtailing periclase
More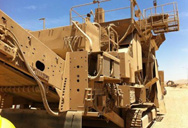
Clinker cooling - INFINITY FOR CEMENT EQUIPMENT
Clinker cooling is necessary because: Hot clinker is difficult to convey. Hot clinker has a negative effect on the grinding Process. The reclaimed heat content of the hot clinker of about 200 kcal/kg, is an important factor lowering the production cost. Proper cooling improves the quality of the cement.
More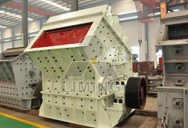
Cement Grinding - Cement manufacturing process - Priya Cement
2023.10.10 OPC is produced by the inter-grinding and blending of 95% clinker with 5% gypsum to a fineness of 280 m 2 /kg. PPC is produced by the inter-grinding and blending of 65% clinker with 30% fly ash and 5% gypsum to a fineness of 320 m 2 /kg. Fineness is a controlled parameter for cement to ensure better hydration and strength development.
More
Effect of clinker grinding aids on flow of cement-based
2014.9.1 Grinding aids (GAs) are increasingly used during cement production to reduce energy consumption and/or optimize clinker factor. This paper seeks to assess the effect of such additions on variations in flow of cement pastes, including static yield stress (τ 0) and viscosity (η).Grinding tests were performed at fixed specific energy consumption
More
Efficiency of grinding stabilizers in cement clinker processing
2013.4.1 Introduction. The amount of energy used in cement flour production is immense. About 110 kWh/t is necessary for cement grinding processes (Sverak, 2004).Given that world cement production in 2011 was 33.0 Mt/year, a total of 3.63 TWh/year goes into cement production.This represents 0.018% of all electric energy,
More
Effect of clinker grinding aids on flow of cement-based
In this study, the effects of four grinding aids (Triisopropanolamine based (TIPA), Triethanolamine based (TEA), Hydroxylamine based (HA), and Calcium nitrate based (CN) grinding aids) in the clinker grinding process were evaluated on the essential characteristics of the produced cement: namely specific surface area (Blaine number), compressive ...
More